Note
Please bear in mind that every situation is unique. These practices are a guideline only, and may need to be adjusted for your specific environment.
When scanning a shaft, raisebore, or ore pass, it is best to use Hovermap in its cage to protect the scanner. Shafts and passes are not ideal environments for flying, as they can be very smooth, with few features. This lack of features can potentially lead to a SLAM slip, which can lead to a crash.
Warning
Please bear in mind that you still need some features to scan a shaft. Completely featureless shafts won’t scan well.
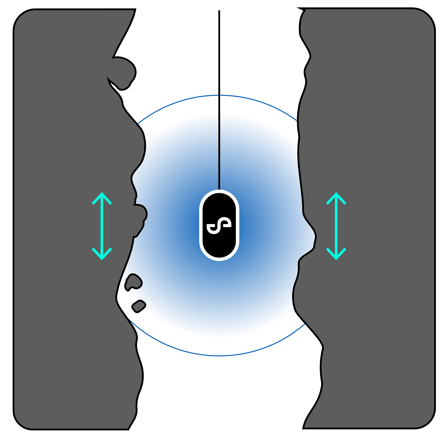
We recommend that you follow this process for the best results.
Step 1: Perform your mission
-
Lower Hovermap in its protective cage slowly towards the bottom of the shaft. A speed of around 1 meter per second is best. The cage will slide along most steep surfaces.
-
If Hovermap becomes stuck on a small ledge, move the lowering cable around gently. The cage should roll out and continue its descent.
-
Avoid hitting the bottom of the shaft. If Hovermap hits the bottom, it will have direct contact with the soil and may become covered in mud. If this happens, it will become “blind” until it can be cleaned. Hovermap is able to deliver great resolution at large distances, so there is no need to get too close. A distance of 10 m should be fine.
-
While scanning, check the live point cloud to ensure that your data is being collected correctly. Do this in the Hovermap App or the Waypoint UI (go to The Hovermap App for more information). You can also do this by connecting to the Hovermap’s Wi-Fi, opening a web browser (on any laptop or Android device), and then navigating to hover.map:8082. This is a good way to check whether you have captured the entire length of the shaft, or whether a second run is required.
-
When you reach the top, stop the scan remotely.
Step 2: Process your data
-
Process your scan data using the Emesent Aura Software. Select the Standard profile for the first job. You may see that the starting point is not aligned with the endpoint of the scan. This is most likely due to the lack of features, especially horizontal features, that would help Hovermap to better determine its position on the Z-axis.
-
If your results are not as desired, you can then change the processing parameters. For a linear scan such as a shaft, we recommend that you make the following changes to the processing parameters:
-
Local Mapping: Voxel size: 0.2
-
Global Registration:
-
Voxel size: 0.2
-
Matching: Max Distance: 5.00
-
-
Note
These processing parameters work more often than not. However, it is still dependent on your specific environment, so they may not yield the desired results. If you don’t get the result you are looking for, play around with the rest of the settings. But be aware that this will increase your processing times significantly.